5.1 胶件排位
胶件排位是指据客户要求,将所需的一种或多种胶件按合理注塑工艺、模具结构进行排列。胶件排位与模具结构、塑胶工艺性相辅相成,并直接影响着后期的注塑工艺,排位时必需考虑相应的模具结构,在满足模具结构的条件下调整排。
从注塑工艺角度需考虑以下几点:
(1)流动长度。每种胶料的流动长度不同,如果流动长度超出工艺要求,胶件就不会充满。(具体参见第二章)
(2)流道废料。在满足各型腔充满的前提下,流道长度和截面尺寸应尽量小,以保证流道废料最少。
(3)浇口位置。当浇口位置影响胶件排位时,需先确定浇口位置,再排位。在一件多腔的情况下,浇口位置应统一。
(4)进胶平衡。 进胶平衡是指胶料在基本相同的情况下,同时充满各型腔。
为满足进胶平衡一般采用以下方法:
A.按平衡式排位(如图5.1.1),适合于胶件体积大小基本一致的情况。
B.按大胶件靠近主流道,小胶件远离主流道的方式排位,再调整流道、浇口尺寸满足进胶平衡 (关于流道、浇口设计详见第九章)。
注意:当大小胶件重量之比大于8时,应同产品设计者协商调整。在这种情况下,调整流道、浇口尺寸很难满足平衡要求。
(6)型腔压力平衡。型腔压力分两个部分,一是指平行于开模方向的轴向压力;二是指垂直于开模方向的侧向压力。排位应力求轴向压力、侧向压力相对于模具中心平衡,防止溢胶产生批峰 。
满足压力平衡的方法:
A.排位均匀、对称。轴向平衡如图5.1.2;侧向平衡如图5.1.3
B.利用模具结构平衡 如图5.1.4 这是一种常用的平衡侧压力的方法,具体的技术要求参见下节。
从模具结构角度需考虑一下几点
(1)满足封胶要求
排位应保证流道、唧咀距前模型腔边缘有一定的距离,以满足封胶要求。一般要求D1≥5.0mm,D2≥10.0mm,如图5.1.5所示。
行位槽与封胶边缘的距离应大于15.mm。
(2)满足模具结构空间要求
排位时应满足模具结构件,如铲鸡、行位、斜顶等的空间要求。同时应保证以下几点:
A.模具结构件有足够强度
B.与其它模胚构件无干涉
C.有运动件时,行程须满足出模要求.有多个运动件时,无相互干涉.如图5.1.6
D.需要司筒的位置要避开顶棍孔的位置
(3)充分考虑螺钉、冷却水及顶出装置
为了模具能达到较好的冷却效果,排位时应注意螺钉、顶针对冷却水孔分的影响,预留冷却水孔的位置。
(4)模具长宽比例是否协调
排位时要尽可能紧凑,以减小模具外形尺寸,且长宽比例要适当,同时也要考虑注塑机的安装要求。
5.2 分模面的确定
5.2.1 分模面选择原则
打开模具取出胶件或浇注系统的面,称之为分模面。分模面除受排位的影响外,还受塑件的形状、外观、精度、浇口位置、行位、顶出、加工等多种因素影响。合理的分模面是塑件能否完好成型的先决条件。一般应从以下几个方面综合考虑:
(1)符合胶件脱模的基本要求,就是能使胶件从模具内取出,分模面位置应设在胶件脱模方向最大的投影边缘部位。
(2)确保胶件留在后模一侧,并利于顶出且顶针痕迹不显露于外观面。
(3)分模线不影响胶件外观。分模面应尽量不破坏胶件光滑的外表面。
(4)确保胶件质量,例如,将有同轴度要求的胶件部分放到分模面的同一侧等
(5)分模面选择应尽量避免形成侧孔、侧凹,若需要行位成形,力求行位结构简单,尽量避免前模行位.。
(6)合理安排浇注系统,特别是浇口位置。
(7)满足模具的锁紧要求,将胶件投影面积大的方向,放在前、后模的合模方向上,而将投影面积小的方向作为侧向分模面;另外,分模面是曲面时,应加斜面锁紧。
(8)有利于模具加工。
5.2.2 分模面注意事项及要求
(1)台阶型分模面
一般要求台阶顶面与根部的水平距D≥0.25,如图5.2.1所示。为保证D的要求,
一般调整夹角“A”的大小,当夹角影响产品结构时,应同相关负责人协商确定。当分模面中有几个台阶面,且H1≥H2≥H3时,角度“A”应满足A1≤A2≤A3,并尽量取同一角度方便加工。
角度“A”尽量按下面要求选用:
当H ≤ 3mm,斜度 α ≥ 5˚; 3mm ≤ H ≤ 10mm,斜度α ≥3˚;
H > 10mm,斜度α ≥ 1.5˚;
某些胶件斜度有特殊要求时,应按产品要求选取。
(2)曲面型分模面
当选用的分模面具有单一曲面(如柱面)特性时,如图5.2.2,要求按图5.2.2a的型式即按曲面的曲率方向伸展一定距离建构分模面。否则,则会形成如图5.2.3a所示的不合理结构,产生尖钢及尖角形的封胶面,尖形封胶位不易封胶且易于损坏。
当分模面为较复杂的空间曲面,且无法按曲面的曲率方向伸展一定距离时,不能将曲面直接延展到某一平面,这样将会产生如图5.2.4a所示的台阶及尖形封胶面,而应该延曲率方向建构一个较平滑的封胶曲面,如图5.2.4b所示。
(3)封胶距离
模具中,要注意保证同一曲面上有效的封胶距离。如图5.2.3a ,5.2.3b所示,一般情况要求D≥3mm
(4)基准平面
在建构分模面时,若含有台阶型、曲面型等有高度差异的一个或多个分型面时,必需建构一个基准平面,如图5.2.5a ,5.2.5b所示。
基准平面的目的是为后续的加工提供放置平面和加工基准。
(5)分模面转折位 如图5.2.6
此处的转折位是指不同高度上的分型面为了与基准平面相接而形成的台阶面。
台阶面要求尽量平坦,图示尺寸“A”一般要求大于15o,合模时允许此面避空。转角R优先考虑加工刀具半径,一般R≥3.0mm。
(6)平衡侧向压力
由于型腔产生的侧向压力不能自身平衡,容易引起前、后模在受力方向上的错动,一般采用增加斜面锁紧,利用前后模的刚性,平衡侧向压力,如图5.2.7所示,锁紧斜面在合模时要求完全贴合。
角度A一般为15°,斜度越大,平衡效果越差。
(7)唧嘴碰面处平坦化
构建分模面时,如果唧嘴附近的分型面有高度差异,必须用较平坦的面进行连接,平坦面的范围要大于唧嘴直径,一般有效面积应大于Ø18mm,如图5.2.6所示
(8)细小孔位处分模面的处理
不论小孔处原身留,还是镶针,一般采取以下方法,对孔位进行构造。为了模具制作简单,建议孔位处镶针,但须经过设计者允许。
A.直接碰穿 如图5.2.9 ,适用于碰穿位较平坦的结构。但对于“键盘”类的按键孔(如图5.2.10a),为了改变有可能产生的“批锋”的方向,常采用插穿形式的结构及尺寸,如图5.2.10b所示。
B.中间平面碰穿 如图5.2.11a,适用于碰穿位较陡峭的结构采用中间平面碰穿的结构可以有效缩短碰穿孔处钢位的高度,改善钢位的受力情况。为避免前、后模偏位,建议采用5.2.11a图示尺寸及结构。图5.2.11b所示结构中,由于在碰穿处产生侧向分力,当碰穿孔较小时,在交变应力的作用下,碰穿孔处的钢位易于断裂,影响模具寿命。
C.插穿 一般不采用,仅仅用在以下所示的情况。
(1)当“a”点与“b”的高度差小于0.5mm时,如图5.2.12a,采用插穿结构。
(2)当“a”点高于“b”点时,如图5.2.12b,采用插穿结构。
当采用插穿结构时,常采用图5.2.12c所示结构及尺寸。封胶面最小距离须保证1.0mm;导向部位斜度A≥5o 长度H≥2.5mm。
(9)避免产生尖钢
当分型线须分割一个曲面时,为了避免产生尖钢,分型面的方向应为分型线上任一点的法线方向。如图5.2.13所示。
(10)综合考虑产品外观要求
对于单个产品,分型面有多种选择时,要综合考虑产品外观要求,选择较隐蔽的分型面。对于有行位分型的成品,行位分型线必须考虑相邻成品的结构,如相邻成品同样需要行位分型,那幺行位分型线应调整对齐;如图5.2.14a;5.2.14b;5.2.14c;如相邻成品不需行位分型,在满足结构的情况下,行位分型线应尽量缩短如图5.2.7d
5.3 模具强度
普通意义上的模具强度包括模具的强度、刚度。模具的各种成型零部件和结构零部件均有强度、刚度的要求,足够的强度才可以保证模具能正常工作。
由于模具形式较多,计算也不尽相同且较复杂,实际生产中,采用经验设计和强度校核相结合的方法,通过强度校核来调整设计,保证模具能正常工作。
5.3.1 强度校核
模具强度计算较为复杂,一般采用简化的计算方法,计算时采取保守的做法,原则是:选取最不利的受力结构形式,选用较大的安全系数,然后再优化模具结构,充分提高模具强度。
为保证模具能正常工作,不仅要校核模具的整体性强度,也要校核模具局部结构的强度。
整体性强度主要针对型腔侧壁厚度,型腔底板厚度,合模面所能承受的压力等几个方面,计算按MQP702中附录D《模具设计验证》执行。实际选用尺寸应大于计算尺寸并取整。
对于其他零部件,如镶件、斜顶、行位、铲鸡、甚至导柱等的强度,根据下面的简单计算进行校核,校核时应从强度与弯曲两个方面分别计算,选取较大的尺寸。(参见《材料力学》上册p174/p212/p259,高等教育出版社,刘鸿文主编)
简化模型如图5.3.1所示
F—杆件所受的力; fy—弹性变形量 MMax最大弯距
D—圆直径
[δ]—允许最大抗弯应力, 王牌钢[δ]=200 Mpa ; 预硬化模具钢[δ]=300~350Pa E=2.1X105 Mpa
5.3.2 提高整体强度
(1)尽量避免凹腔内尖角,如图5.3.2 增加圆角对增强侧壁刚度有较明显的帮助,另外也可减小应力疲劳,延长模具使用寿命,所以前后模框的四个角必需制成圆角,前后模中的镶件也应尽力避免尖角的出现
(2)增加锁紧块,减少弹性变形。如图5.3.3
(3) 减小方铁间距,如图5.3.4
为减少弹性变形量y,在可满足顶出的条件下,尽量减小方铁间距L,同时将型腔压力移向方铁,尽量保证图示要求。
(4)注意模肉镶拼时的方向,选择合理的镶拼结构。如图5.3.5所示。
(5)增加撑头 如图5.3.6
撑头的布置需根据实际情况而定,数量尽可能多,装配时两端面必需平整,且所有撑头高度需一致。
撑头常用规格:Ø38mm Ø45mm
撑头材料:王牌钢
5.3.3 加强组件强度
对于模具而言,组件的强度与整体强度同等重要,组件的受力情况复杂,除通过简单计算进行校核外,必须遵守一个基本原则:强度最强,即是说在结构空间容许时,组件结构最大化。
下面列举几类可提高组件强度的方法。
(1)修改胶件结构,避免产生尖钢、簿钢。由于胶件结构不合理,将引致模具尖钢、簿钢时,应与产品设计协商解决。
(2)增加锁紧块 ,改进模具结构,提高组件(铲鸡)强度。如图5.3.8
(3)利用模胚刚性,提组件(铲鸡)强度。 如图5.3.9
(4) 改善组件结构,增大组件尺寸,提高组件强度。
图5.3.10所示中,左图“W1”较小,易变形;右图不仅改善了组件结构,并增大了组件尺寸“W2”,有利于提高强度。在此结构中,为了减小变形,还应该增加图示“R”处的圆角,减小“H”的尺寸, “H”一般取8.0~10.0mm.
(5)高型芯或长型芯端部定位,提高强度,减少型芯变形。
在具有高型芯或长型芯的模具结构中(如图5.3.11a),设计时应充分利用端部的通孔对型芯定位,如图5.3.11b结构所示。端部不允许有通孔时,应同模具设计负责人协商解决。
(6)利用镶拼结构,提高局部强度。
在胶件的细小结构处,如果存在薄钢或应力集中点(如图5.3.12a),设计时应将此处设计成镶拼结构,以消除应力集中点,减小疲劳损坏,也有利于对镶件进行热处理而增加强度,如图5.3.12b所示。
5.4 成形零件设计
模具零件按其作用可分为成形零件与结构零件,成形零件是指直接参与形成型腔空间的结构件,如凹模(型腔)、凸模(型芯)、镶件、行位等;结构零件是指用于安装、定位、导向、顶出以及成形时完成各种动作的零件,如定位圈、唧咀、螺钉、拉料杆、顶针、密封圈、定距拉板、拉勾等等。常用结构零件参见下节。成形零件设计时,应充分考虑胶料的成形收缩率、脱模斜度、制造与维修的工艺性等。
5.4.1 胶料的成形收缩率
胶料的成形收缩受多方面的影响,如胶料品种、胶件几何形状及大小、模具温度、注射压力、充模时间、保压时间等,其中影响最显著的是胶料品种、胶件几何形状及壁厚。不同的胶料具有不同的收缩率范围(参见第二章,常用塑料),具体的收缩率根据推荐值而定,如有改动,需相应负责人确定。
值得注意的是,对同一胶件增加收缩值时,3D设计和2D设计所选用的参考点应相同,否则将会使3D和2D设计不统一。
5.4.2脱模斜度
合理的脱模斜度是便于脱模、获取高质量表面要求的必要条件。在胶件设计时,一般都会给出较为合理的脱模斜度。但由于有时考虑不周,胶件选用或形成了不合理的脱模斜度,这将势必影响胶件的表面质量,所以在模具设计时应对胶件的脱模斜度进行检查,并与相关的负责人协商解决不合理的地方。以下是对脱模斜度的一般要求:
(1)常用胶料如ABS、HIPS、PC、PVC等,胶件外表面的脱模斜度参照下述选用:
外表面为光面的小胶件,脱模斜度 ≥ 1˚;大胶件的脱模斜度 ≥ 3˚
外表面蚀纹面Ra < 6.3,脱模斜度 ≥ 3˚;Ra ≥ 6.3,脱模斜度 ≥ 4˚
外表面火花纹面Ra < 3.2,脱模斜度 ≥ 3˚;Ra ≥ 3.2,脱模斜度 ≥ 4˚
(2)不论胶件内表面的骨位、柱位是否设计有脱模斜度,在进行模具设计时,都应按下述要求增加或修改脱模斜度。
骨位根部的厚度小于0.5t,(“t”为胶件的壁厚);骨位顶部的厚度应大于或等于0.8mm,具体的脱模斜度依照已确定的厚度差及骨位的高度而定。若骨位长度方向两侧需要脱模斜度时,在不影响胶件内部结构的情况下,应选取较大的脱模斜度。
柱位的要求按第三章第三节的内容对其进行修改。
(3)在增加或修改擦、碰穿位的脱模斜度时,按第五章第二节中对台阶型分模面的要求选用, 影响胶件结构时,应与相关负责人协商解决。
5.4.3成形零件的工艺性
模具设计时,应力求成形零件具有较好的装配、加工及维修性能。为了提高成形零件的工艺性,主要应从以下几点考虑:
(1)不能产生尖钢,薄钢 如图5.4.1a;5.4.1b;5.4.1c
(2)易于加工
易于加工是成型零件设计的基本要求,模具设计时,应充分考虑每一个零件的加工性能,通过合理的镶拼组合来满足加工工艺要求。例如,为了胶件止口部位易于加工,一般采用图5.4.2a、5.4.2b所示的镶
拼结构。其他组合方式或不做镶拼均为不合理的设计结构。
(3)易于修整尺寸及维修
对于成型零件中,尺寸有可能变动的部位应考虑组合结构,如图5.4.3所示;对易于磨损的碰、擦位,为了强度及维修方便,应采用镶拼结构。
(4)保证成型零件的强度 (参见第五章第三节)
(5)易于装配
针对镶拼结构的成型零件而言,易于装配是模具设计的基本要求,而且应避免安装时出现差错。对于形状规整的镶件或模具中有多个外形尺寸相同的镶件,设计时应考虑避免镶件错位安装和同一镶件的转向安装。常常采用的方法是镶件非对称紧固或定位 。如图5.4.4b所示。
在图5.4.4a中,紧固位置对称,易产生镶件1与镶件2的错位安装,同一镶件也容易转向安装。在图5.4.4b中,每个镶件的紧固位置非对称布置,且镶件1与镶件2的紧固排位也不相同,从而避免产生错位安装及同一镶件转向安装。另外,为了避免错位安装,也可采用定位销非对称排布的方法。
(6)不能影响外观
在进行成型零件设计时,不仅要考虑其工艺性要求,而且要保证胶件外观面的要求。胶件是否允许夹线存在是决定能否制做镶件的前提,若允许夹线存在,则应考虑镶拼结构,否则,只能采用其他结构形式。图5.4.5中,胶件表面允许夹线存在,则可以采用镶拼结构,以利于加工;图5.4.6中,胶件正表面不允许夹线存在,为了利于加工或其他目的,将夹线位置移向侧壁,从而采用镶拼结构。图 5.4.7中,当圆弧处不允许夹线时,更改镶件结构,将夹线位置移向内壁。
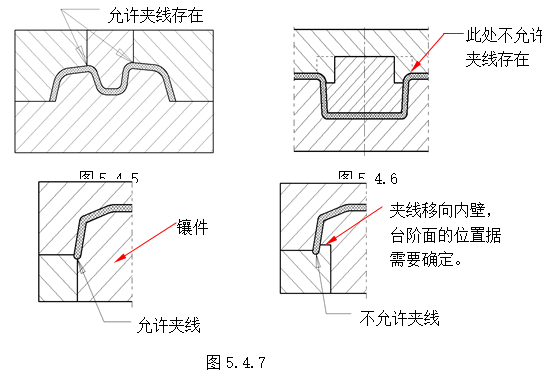
(7)综合考虑模具冷却。成型零件采用镶拼结构后,若造成局部冷却困难,应考虑采用其它冷却方法或整体结构。
5.5 常用结构件设计
5.5.1 定位圈
(1)基本形式,如图5.5.1中“4”所示
(2)装配形式,如图5.5.1
螺钉:M6x20.0mm 数量: 2 个
(3)常用规格 Ф35xФ100x15
(4)特殊情况
当模具需要使用隔热板时,采用加厚的定位圈,如图5.5.1b所示。一般选取规格为 Ф70xФ100x25的定位圈。
双色模中的定位圈的规格参阅第十二章。
5.5.2 唧咀
唧咀通常被分为大水口唧咀及细水口唧咀俩大类。大水口唧咀指使用于两板模的唧咀,细水口唧咀是指使用于三板模的唧咀。下面分述其具体的使用情况。
A.大水口唧咀
(1)常用基本形式,如图5.5.2。规格类型请参阅第十五章。
(2)大水口唧咀的选用方法
大水口唧咀通常根据模具所成型胶件所需胶量的多少、所需唧咀的长度选用。所需胶量多时,选用较大的唧咀;反之则选用较小的类型。根据唧咀的长度选取不同的夹角“A”,以便唧咀尾端的孔径能与主流道的直径相匹配。一般情况下,根据模胚大小选取,模胚3535以下,选用D= Ø12的类型;模胚3535以上,选用D= Ø16.0的类型。
(3)装配方式
基本装配方式如图5.5.1所示。
螺钉规格:M4X20mm 数量:1
若为了缩短唧咀的长度“L”,建议采用图5.4.3的装配方式,同时必须加强前模紧固。当面板与主流道的间距D≥60mm时,
建议采用此种方式。
B.细水口唧咀
(1)基本形式如图5.5.4零件“2”所示,当使用隔热板时,H=20.0mm;无隔热板时H=10.0mm
(2)装配形式如图5.5.4
装配要求:锥面配合高度“H1”范围内须紧密贴合,一般H1≥8.0mm
保证图示尺寸“20.0mm”
螺钉选择 规格:M8x20.0mm 数量:4
(3)常用规格
常用规格参见第十五章。十五章中所列规格均为无隔热板时的尺寸,若需隔热板时,请按上述要求增加图5.5.4中“H”的尺寸。
(4)简化形式 如图5.5.5
特点:制作简单,将大水口唧咀头部加工出锥面后即可使用。
缺点:主流道太长,浪费胶料,水口板与模胚A板的分型距离较大。
适用对象:
A.模胚较小,一般在3030规格以下使用。
B.使用普通形细水口唧咀时,拉料杆难于固定。这样就可避免为满足拉料杆的布置而增大模具尺寸。
5.5.3 紧固螺钉
模具中常用紧固螺钉主要分为内六角圆柱头螺钉(内六角螺钉),内六角平端紧定螺钉(无头螺钉)及六角头螺拴。常用规格参见第十五章。
在模具中,紧固螺钉应按不同需要选用不同类型的优先规格,同时保证紧固力均匀、足够。下面将各类紧固螺钉在使用中的情况加以说明。
A. 内六角圆柱头螺钉(内六角螺钉)
内六角螺钉的优先规格: M4,M6 ,M10,M12
内六角螺钉主要用于前、后模模料,型芯,小镶件及其它一些结构组件。除前述定位圈、唧咀所用的螺钉外,其它如镶件、呵裙、固定板等所用螺钉以适用为主,并尽量满足优先规格,用于前、后模模料紧固的螺钉,选用时应依照下述要求:
规格:模料宽度≤300mm选用M10 模料宽度>300mm选用M12
数量:模料长度≤300mm使用4个螺钉;模料长度>300mm而且≤500mm使用6个螺钉;模料长度>500mm而且≤800mm使用8个螺钉。
中心距:按下列两种方式选择 参见图5.5.6
当选用M10 时 W1=10.5mm—14.5mm
L1=15n OR 20n n表示倍数
当选用M12 时 W1=12.5mm—13.5mm
L1=25n OR 30n n表示倍数
B. 内六角平端紧定螺钉(无头螺钉)
无头螺钉主要用于镶针、拉料杆、司筒针的紧固。如图5.5.7 ,在标准件中, Ød和ØD相互关联,Ød是实际上所用尺寸,所以通常以Ød作为选用的依据,并按下列范围选用。
a.当Ød≤3.0mm或9/64″时,选用M8
b.当Ød≤3.5mm或5/32″时,选用M10
c.当Ød≤7.0mm或3/16″时,选用M12
d.当Ød≤8.0mm或5/16″时,选用M16
e.当Ød≥8.0mm或5/16″时,用压板固定(具体结构参见第八章8.2节)
C.六角头螺拴
六角头螺拴仅作为垃圾钉的替用品,使用品种较为单一,一般使用M10X20、M12X20两种形式。
使用数量据下述要求而定。
当模坯顶针板长度≤350时,选用数量4个;当坯顶针板长度≥400时,选用数量6 个;当模坯顶针板长度≥600时,选用数量8个 。
5.5.4 顶针
A.顶针布置原则
(1)顶针布置应使顶出力尽量平衡。结构复杂部位所需脱模力较大,顶针数量应相应增加。
(2)顶针应设置于有效部位,如骨位、柱位、台阶、金属嵌件、局部厚胶等结构复杂部位。骨位、柱位两侧的顶针应尽量对称布置,顶针与骨位、柱位的边间距一般取D=1.5mm,如图5.5.8所示,另外,应尽量保证柱位两侧顶针的中心连线通过柱位中心。
(3)避免跨台阶或在斜面上设置顶针,顶针顶面应尽量平缓,顶针应布置于胶件受力较好的结构部位。如图5.5.9所示。
(4)在胶件较深的骨位(深度≥20mm)或难于布置圆顶针时,应使用扁顶针。需要使用扁顶针时,扁顶针处尽量采用镶件形式以利于加工。如图5.5.10
(5)避免尖钢、薄钢,特别是顶针顶面不可碰触前模面。如图5.5.11
(6)顶针布置应考虑顶针与运水道的边间距,避免影响运水道的加工及漏水。具体要求参见第十章10.2节。
(7)考虑顶针的排气功能,为了顶出时的排气,在易形成抽真空的部位应布置顶针。例如型腔较大平面处,虽胶件包紧力较小,但易形成抽真空,导致脱模力加大。
(8)有外观要求的胶件,顶针不能布置在外观面上,应采用其它顶出方法。
(9)对于透明胶件,顶针不能布置在需透光的部位。
B.顶针选用原则
(1)选用直径较大的顶针。即在有足够顶出位置的情况下,应选用较大直径、且尺寸优先的顶针。
(2)选用顶针的规格应尽量少。选用顶针时,应调整顶针的大小使尺寸规格最少,同时尽量选用优先的尺寸系列。尺寸规格参见第十五章15.1节。
(3)选用的顶针应满足顶出强度要求。顶出时,顶针要承受较大的压力,为避免小顶针弯曲变形,当顶针直径小于2.5mm时,应选用有托顶针。
5.5.5司筒
A.选用司筒的条件
(1)柱位高度≥20mm;但当柱位高度要求严格时,不能使用司筒。例如VTT公司的电话模具。
(2)柱位处结构复杂,布置顶针困难;
(3)透明件,除柱位外,其它位置不允许顶针痕迹;
B.对司筒的要求
(1)一般情况下,司筒壁厚须 ≥1.0mm
(2)所定购司筒长度等于实际所需长度加5.0mm~10.0mm,并取整成以“5、0”结尾的优先尺寸
(3)司筒针随司筒一起配套定购,并注意司筒针的长度
注:无头螺钉的选取参见第五章5.5.3节。
5.5.6 密封圈
密封圈的常用规格参见第十五章15.5节。
密封圈的装配方式参见第十章10.2.2节。
5.5.7拉料杆
拉料杆按其结构分为勾形拉料杆(如图5.5.12)和圆头形拉料杆(如图5.5.13),勾形拉料杆主要用于确保将流道、胶件(如电池兜部位)留在后模一侧,圆头形拉料杆主要用于三板模、推板模,使流道留于流道推板、推板一侧。

拉料杆在使用中应主意以下几点:
(1)一套模具中若使用多个勾形拉料杆,拉料杆的勾形方向要一致。
(2)流道处的勾形拉料杆,必须预留一定的空间作为冷料井,如图5.5.12,一般予留尺寸如图。
(3)使用圆头形拉料杆时,应注意图5.5.14中所示尺寸“D”、“L”。若尺寸“D”较小,拉料杆的头部将会阻滞胶料的流动;若尺寸“L”较小,流道脱离拉料杆时易拉裂。
增大尺寸“D”的方法:
采用直径较小的拉料杆,拉料杆直径一般取Ø=3.0mm;减小“H”,一般要求H≤3.0mm;增大“R”的尺寸。
增大尺寸“L”的方法:
在拉料杆周围加大流道尺寸,如图5.5.16增加一“Ød”的圆台。
5.5.8 垃圾钉
在模具中,六角头螺拴通常被用做垃圾钉使用。具体参见第五章5.5.3节。
5.5.9 弹簧
模具中,弹簧主要用作顶针板、行位等活动组件的辅助动力,不允许单独使用。模具用弹簧现已标准化,下表是模用弹簧的基本技术规格。
模具中常用的弹簧是轻载的兰弹簧。如果模具较大,顶针数量较多时,必须考虑使用重载弹簧。轻荷重弹簧选用时应主意以下几个方面:
(1)预压比:一般要求为弹簧自由长度的10~15%,直径较大的弹簧选用较小的预压比,直径较小的弹簧选用较大的预压比。
在选用模具顶针板回位弹簧时,一般不采用预压比,而直接采用预压量,这样可以保证在弹簧直径尺寸一致的情况下,施加于顶针板上的预压力不受弹簧自由长度的影响。预压量一般取10.0~18.0mm。
(2)压缩比:一般要求压缩比在40%以下,压缩比越小,使用寿命越长。
(3)弹簧分布要求尽量对称。
(4)弹簧直径规格根据模具所能利用的空间及模具所需的预压力而定,尽量选用直径较大的规格。常用规格参见第十五章15.3节。
当模胚尺寸大于5050时,须选用Ø51.0mm的弹簧。
弹簧自由长度应根据压缩比及所需压缩量而定。
模具回位弹簧自由长度(L)的计算方式:(如图5.5.15所示)
H1—胶件需顶出高度
B—弹簧预压后的长度,B=L - 预压量。预压量通常取10~15mm
L = (K+预压量)/压缩比
5.5.10定距拉板
(1)装配形式。如图5.5.16所示
(2)技术要求:D1一般取10~12mm;D2的尺寸应稍大于流道在开模方向上的投影总长度,但不能小于110mm;D3要求大于1.0mm;D4一般取25mm左右,其他尺寸参靠图示
(3)材料:选用王牌钢
5.6 模具图纸规范
采用第三视图格式,标识如图5.6.1
5.6.2.图纸编号
图纸编号按TLWI07042规定执行。
5.6.3.基准标识
(1)基准标识的类型
基准标识的目的是为了统一设计、加工时工件的基准及摆放方向。目前采用以下两种形式的标记方式:
A.单边基准
单边基准是指设计、加工时,以工件相邻两直角边为基准并按一定的方向摆放,标识标记及摆放方向如图5.6.2所示。
B.中心基准
中心基准是指设计、加工时,以工件的中心线为基准并按一定的方向摆放,标识标记及摆放方向如图5.6.3所示。
(2)标识位置及尺寸 如图5.6.2;5.6.3
注:当R较大时采用括号内尺寸
(3)标识要求:
A.模具图纸(包括装配图、前模图、后模图、呵孔呵裙图、顶针运水图)和前后模上应有此标识,无须标注尺寸。
B.钳工将模料配入模框后,立刻做此标识。
C.加工过程中如破坏了此标识,请马上补做。
D.设计、编程、加工时,工件均应按图5.6.2形式摆放。
5.6.4 图纸输出要求
1.标识模具设计时的基准类型。
2.明确胶件基准线与模具基准线的距离,并于其外围加一粗方框以做警示。
3.清楚表示典型截面的装配结构,分模面形状,外形尺寸 。
4.标明前、后模料,呵孔、呵裙等的最大外形尺寸。如果呵孔上有止口,需做剖图并标明详细尺寸。
5.标识枕位、镶件等的形状尺寸、装配方式。
6.注明紧固螺钉的位置、大小。
7.标注行位机构装配的详细尺寸,行程须用粗方框以做警示。
8.标注流道、浇口详细尺寸,并做剖面。
9.如实反应顶针布置情况,如有顶针图时,装配图中顶针排布、大小尺寸可不标注。标明需钳工制作的各柱位的详细尺寸
10.绘制模具运水排布,注明各组运水的入水口、出水口,并使用IN1、IN2… OUT1、OUT2…等表示。如无运水图时,需注明运水孔的大小及位置尺寸。
11.标注回位弹簧排布尺寸、大小及装配尺寸。
12.标注撑头排布尺寸、大小。
13.在一模多件的模具中,需注明各胶件的P/N号。
14. 如无前、后模图时,装配图中应标注重要尺寸及公差,尺寸旁边做序号标记
并记录在图框栏中,以便钳工检测。有前、后模图时,重要尺寸及公差的标识放在前、后模图中。重要尺寸包括成品图中有公差要求的尺寸、模具中需要控制的尺寸等。
15.不论图纸为何种版本,应在图框栏右上角“简要说明”栏中对版本进行简单描述。
16.模具图升版时,更改内容旁需有升版标记,如
、
等。若仅为位置尺寸更改,新尺寸旁标识升版标记;若成品形状更改,更改部位用“粗双点划线”圈示,并于“粗双点划线”旁标识升版标记。